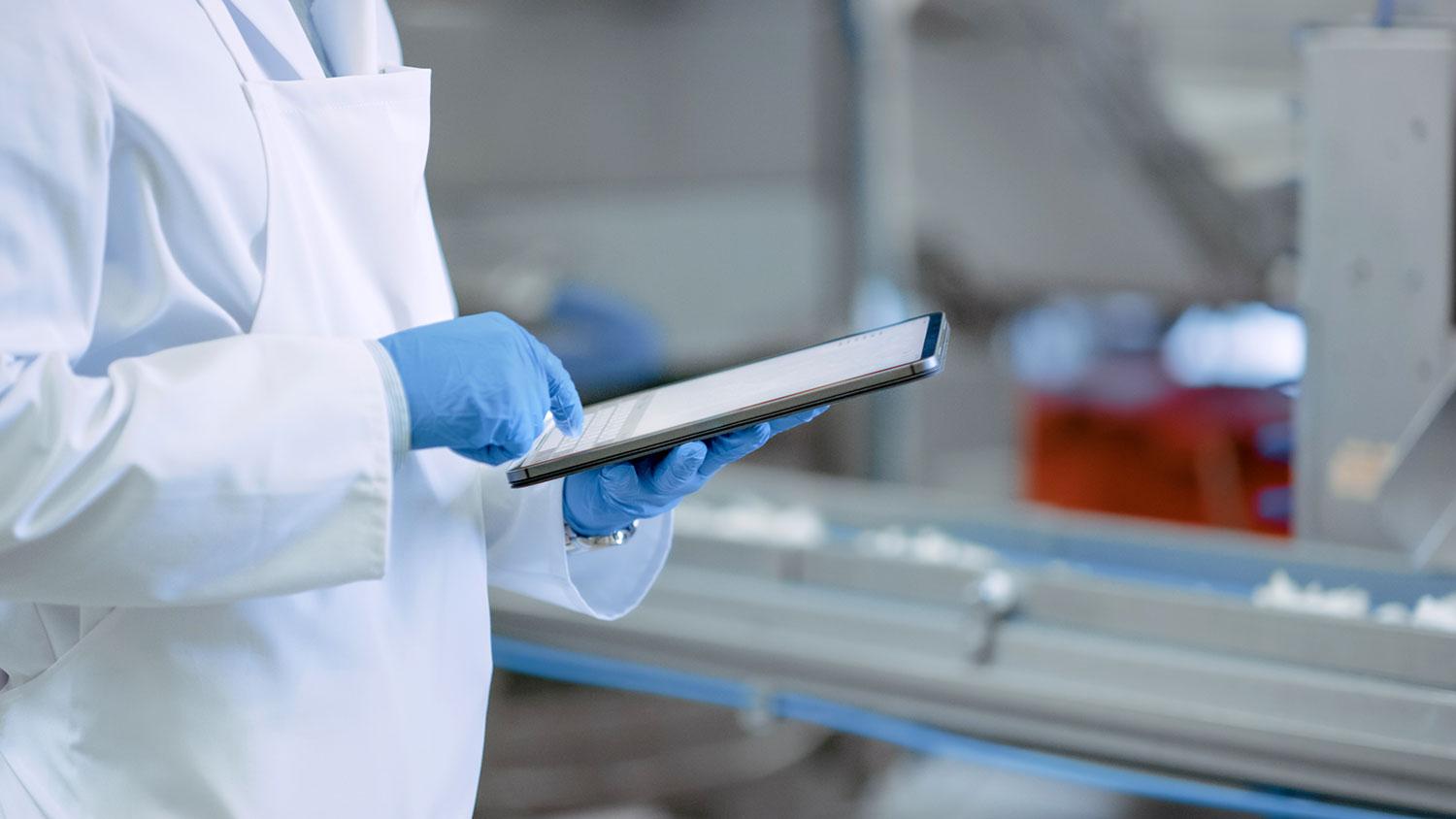
Vapor10 Quality Control
The most important part in production is quality control. Quality control in the production process is divided into three parts.
- Quality control of raw materials.
- Product quality control during production.
- Quality control of the final product.
At Vapor10 company, having a specialized laboratory, we carefully follow all three stages.
Quality control of raw materials
This is a measure to check and verify the quality of raw materials with the analysis sheet of each material. According to the claim of our colleagues, who are the suppliers of our raw materials, each material must have specific characteristics that are mentioned in the analysis sheet, but various factors may cause errors in this case. Improper transportation, improper storage, laboratory error in raw material manufacturing company and other cases. According to the laws of manufacturing and quality control, every manufacturing company must recheck the accuracy of information and the quality of raw materials, either personally or through outsourcing. We at Vapor10 company do this in our own laboratory. A team consisting of several chemists and a printing technical inspector inspects and validates all materials according to the quality plan forms. Bottles, glycerin, propylene glycol, all essential oils, deionized water, preservatives, product packages and labels, and all materials used in the manufacturing process are reviewed here. Also, in our specialized laboratory, we validate and verify all our measurement tools through outsourcing. This is done twice a year by sending to the company’s headquarters in Germany so that any possible errors can be controlled through external testing.
Product quality control during production
According to the quality plan forms, each product must have certain physical and chemical characteristics during production. Also, the construction tools are under strict supervision at this stage. The tools that generate heat, mixers, centrifuges, homogenizers, weight meters and volume meters, tools that generate high level pressure and all accessories during construction are included in this inspection process. If there is any error, the production process will be stopped until the problem is completely resolved by the quality supervisor.
Quality control of the final product
The final product will be analyzed for quality in several parts. The first part is the conformity of the product with the reference standards that the company has considered. Standards such as the amount of essential oil, the color of the final product and others. The second part is to check the packaging of the product in the bottle. The third part is labeling and product technical information. All parameters of the final product must be consistent with the quality plan forms. In all production series, this information is recorded and maintained in our inspection forms according to the ISO process.
We assure you that from the moment of the start of production to the final product, all work steps are under a strict quality control system and all the efforts of the production team are to produce a product with stable quality in different production series.